Electric motors are essential components in a wide range of industries and applications, from industrial machinery to household appliances. Over time, these motors may require rewinding to replace worn or damaged windings, which can affect their performance and efficiency. Electric motor rewinding can help extend the life of these valuable assets and ensure they continue to operate at peak performance levels. In this article, we’ll explore some best practices in motor rewinding that can help ensure a successful outcome.
Determine The Cause of Failure
Before undertaking any rewinding work, it’s important to determine the cause of the motor failure. Different types of failure, such as electrical, mechanical, or environmental, may require different solutions. For instance, if the motor has overheated, the rewinding process may require the use of wire with a higher temperature rating. Determining the cause of failure will also help in identifying any other issues that need to be addressed to avoid future problems.
Choose The Right Wire
Choosing the correct wire for rewinding is essential for ensuring the motor operates efficiently. The wire should have the correct gauge, insulation class, and temperature rating. High-quality wire should be used to ensure a longer service life and better performance. Some manufacturers also provide recommendations for wire specifications, which can be used as a guide.
Ensure Proper Winding Tension
Proper winding tension is critical to ensuring the motor operates correctly. Too much or too little tension can cause damage to the wire, which may result in future problems. The winding tension should be uniform and should not cause any stress on the wire or the motor’s components.
Follow Manufacturer’s Guidelines
Motor manufacturers provide specific guidelines for rewinding their motors, including recommended wire size, insulation class, and winding techniques. Following these guidelines will ensure the motor operates at peak efficiency and reliability.
Use Quality Materials
Using high-quality materials, such as wire, insulation, and varnish, is critical for ensuring the motor operates correctly. Using subpar materials can result in reduced performance, increased wear and tear, and a shorter service life. Quality materials may cost more initially, but they will pay off in the long run by reducing maintenance costs and downtime.
Properly Insulate The Windings
Proper insulation is critical for preventing electrical arcing and protecting the windings from environmental factors, such as heat and moisture. The insulation should be applied uniformly and should not have any air pockets or gaps. The insulation class should also match or exceed the motor’s original specification.
Conclusion
By adhering to best practices in motor rewinding, mechanical and electrical services can ensure their motors continue to operate effectively and efficiently for years to come.
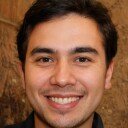
I like to give reasonable advice on budgeting to people with any income level. I currently live in Portland, Oregon and am available for freelance assignments and speaking engagements.